-
Nutrivend selects Forterro’s Orderwise to support online expansion and streamline operations - April 11, 2025
-
ARROWXL LAUNCHES AMBITIOUS ZERO WASTE ROADMAP - April 8, 2025
-
THE BCMPA’S NEW CAMPAIGN DRIVES OUTSOURCING SUCCESS IN Q1 - April 7, 2025
-
BLACKOUT TECHNOLOGIES TARGETS TELEMATICS-INTEGRATED MOBILE DEVICE BLOCKING TO COMBAT SMARTPHONE DISTRACTION - April 1, 2025
-
OpenADR Alliance announces first OpenADR 3.0 certified products with EVoke Systems, E.ON Energy and Universal Devices - March 25, 2025
-
Growing fulfilment and contract packer appoints new Managing Director - March 25, 2025
-
When is it time to invest in a WMS? Understanding the key trigger points - March 25, 2025
-
eCapital helps Vantage Recruitment on its journey to financial success - March 24, 2025
-
Hugo Beck Celebrates 70 Years of Packaging Innovation with Open House Events - March 20, 2025
-
PROLOG FULFILMENT SUPPORTS LUNA DAILY’S COMMITMENT TO BETTER BODY CARE FOR ALL WOMEN - March 19, 2025
Hyster-Yale: Integrating Fork Lift Trucks With RFID
RFID is widely used by logistics and distribution companies to track goods, containers or pallets. It provides a way of quickly and accurately locating and identifying things. But control of the goods isn’t the only use that RFID is finding in logistics and distribution.
The control of fork lift trucks within and around distribution centres is an important issue for warehousing and logistics organisations. Improved control of automated and manned handling equipment allows greater customisation of the equipment within the application to improve productivity. Hyster-Yale Materials Handling, the manufacturer of Hyster® and Yale® fork lift trucks, devised an innovative way to improve the control and management of materials handling equipment.
Using RFID, they found a more intelligent, more efficient way of letting their trucks know just where they were in relation to the world around them. Working with CoreRFID, they created a truck movement control system that identifies a truck’s location within a warehouse and uses that information to control the truck’s operation, acting as driver aids for the operator, providing a more relaxed operation and increase in productivity.
Improving Productivity In Warehouses
Hyster-Yale is one of the world’s leading suppliers of fork lift trucks and similar materials handling equipment. From its years of experience, Hyster-Yale has built up an understanding of the factors that cause truck down-time and otherwise reduce the productivity of warehouse handling equipment fleets. Trucks have to operate in locations where speed restrictions apply and where load handling limits have to be observed as well. Distribution and Logistic companies are looking to increase productivity and reduce down time while providing an ergonomic work place for their operators. Having driver aids that can assist the operator provides many of these features.
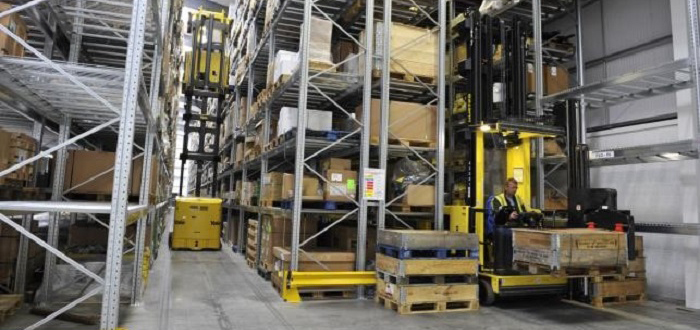
Image: Warehouse trucks have to navigate narrow aisles and avoid collisions with racking.
Modern trucks have on-board electronics to assist the operator in proper use, but to be most effective; these systems depend on knowing the truck’s location. Various methods had been tried to allow the truck’s on-board communication system to understand the warehouse surroundings. While in the future a solution based on artificial intelligence and visual sensing might prove practical, today, the best solution to the problem has proven to be based on the use of RFID.
As a result, Hyster-Yale offers a range of RFID-equipped trucks that can sense their position and limit truck operations such as speed or load lift height depending on where the truck is in the warehouse.
Hyster-Yale started working with the technology in 2010, choosing CoreRFID as their technology partner with the RFID expertise to help them create the best solution for Hyster-Yale clients, worldwide. Installations of systems using the RFID enabled system started in 2013 and the two companies have worked together ever since.
How RFID Helps Hyster-Yale’s Clients
Hyster-Yale created a new system for their trucks which uses RFID tags installed in the warehouse premises and readers installed on their trucks. The readers are linked to on-board “driver assist” truck control systems. The tags are installed in small drilled holes in the warehouse floor. They provide a means for a truck to uniquely identify an aisle within a warehouse, and then, within each aisle, determine speed-controlled areas and areas of lifting limits (for example to assist the operator in avoiding the truck extending its lifting forks upwards and striking roof beams). The system can set limits or enable/disable truck functions.
So, while the truck is driven by a human operator, the on- board system provides assistance and information. Hyster-Yale designed the system for easy installation, reflecting the common problems of their users.
Slow-down zones can be used in areas of restricted visibility, where exiting an aisle, or where there are uneven floors or narrow access, for example.
Lift limit zones can be used to assist operators with overhead obstructions.
The on-board lift truck system is supported by a PC based application that can work with the various tags to set the control areas and the limits that apply to the trucks.
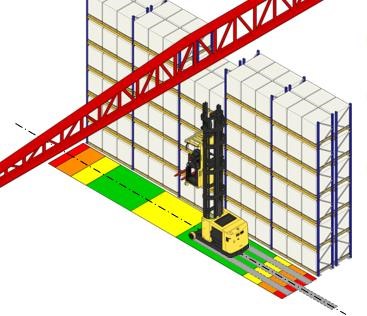
Image: Hyster-Yale’s system lets trucks automatically detect slow, caution and unrestricted speed zones, as well as locations with height restrictions.
CoreRFID worked with Hyster-Yale to identify the most appropriate RFID technology – in this case, low frequency EM4200 compatible tags – and have supplied Hyster-Yale with the location-identifying tags and the readers that Hyster-Yale connects to its on-board truck management systems.
The system uses zones within the truck operating areas. These are delineated by RFID tags that are buried in small holes drilled in the floor of the warehouse. The tags can be sensed at distances of 50cm or so, providing an accurate location for the vehicle – more accurate than would be possible with GPS, for example. From the location information, the driver assist system is able to limit the truck’s speed to the appropriate one for the zone and for what the truck is doing. In the longer term, these problems might be solved by AI-based technologies, but today, this is a low-cost, simple and reliable alternative that does not depend on complex recognition systems.
Hyster-Yale cites a number of benefits over earlier systems that had tried to do similar things using magnetic sensors or reflective tags. The RFID approach has a lower installation cost compared with magnets with little to no down time of the application and has the potential for lower whole-life costs through reduced floor damage, fewer mechanical shocks to trucks, flexibility for future re-configuration, extension or reduction of warehouses, and the ability to add future features with software updates. The system also avoids the problem with systems based on reflective tags which can be inadvertently covered up, rendering the system useless. Unlike other systems, the RFID solution works by reading the tag information and then defining all of the parameters that the truck needs to know for that aisle. This means if in the unlikely event the truck doesn’t see the tag, then the truck remains in a restricted mode.
“The RFID based location system enables more intelligent driver assist features than competitive products. CoreRFID has been instrumental in helping us to create and supply it.” Ron Farr, Manager Warehouse Solutions, Hyster-Yale
For more info please contact Richard Harrison on 07752 389 745 or [email protected]